A brick-in-sand patio is easy to build and requires just a few basic skills and about 2 days’ work.
It’s a great way to expand the living area of the home and provide an entertainment area for family and friends. #DIYPatio #HomeImprovement
The same brick-in-sand method can be used to provide a convenient, flat pathway that keeps your feet out of the mud on a rainy day.
Or create a walkway around the house to provide a firm, smooth surface. Path building is a great project for homeowners of all skill levels. #Pathway #HomeProjects
A brick paver walkway is set on a solid bed of gravel and sand. It will stay flat and smooth even under heavy use, and unlike concrete, it won’t crack due to soil movement.
By using different bonding patterns, you can add a unique decorative dimension.
If you choose a rustic brick, use the colour variations to create a natural and unique effect. #BrickWalkway #DecorativeDesign
The installation of clay brick paving is a relatively quick and easy process and, once laid, the pavers can be used immediately. #QuickInstallation #ClayPaving
Low Cost, Easy Maintenance
A patio can be created with many materials, but clay brick pavers are the material of choice for their natural beauty, durability, and superior colour retention even when wet.
Pavers are produced in different colours, dimensions, and thicknesses.
Typically, thinner pavers (50mm or less) are suitable for low traffic applications such as domestic driveways, patios, and paved walkways. #ClayPavers #DurableMaterials
A paved patio is low maintenance. Clay brick pavers laid on a sand bed will adjust to accommodate the movement of any underlying earth materials, preventing cracks.
The durability of clay pavers means replacement is generally unnecessary, however, if there is any damage to a paver, they are easily replaced.
It is simply a matter of removing the damaged paver and replacing it with a new one, thereby decreasing any future maintenance costs.
Unlike a timber deck, paved areas are hard-wearing, easy to clean, and do not need any expensive year-on-year upkeep. #LowMaintenance #EasyToClean
Why Clay Pavers?
Clay pavers are renowned for their colour integrity which comes from natural pigmentation as opposed to an artificial additive.
They retain the original colour without being affected by any form of ultraviolet light, creating an unmatched richness and warmth for any paved area.
The shape of each paver has a natural, textured character that complements any style of home. #NaturalBeauty #ColorIntegrity
The skid-resistant features of clay brick pavers make it an excellent solution for any heavily trafficked areas that could become wet, such as pathways or even swimming pools.
Clay brick can withstand high temperatures so it is most suitable where you would like to braai. #SkidResistant #HighTemperature
Design
Choose your paving bonding pattern – see below figure for ideas.
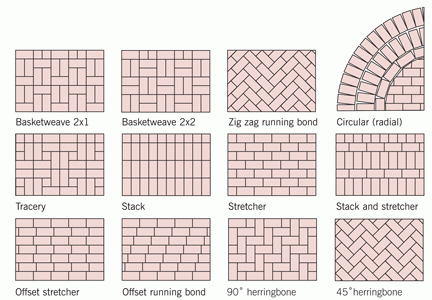
- Basketweave and stack patterns are easy to lay.
- Stretcher patterns are attractive but will require some bricks to be cut.
- Diagonal herringbone patterns are ideal for patios that are an unusual shape but will require a lot of cutting.
- Slight colour changes can add to the design.
- Set full bricks at the outer edge to form a “soldier” row i.e. place the outer row perpendicular to the inner rows to form a natural border.
PavingPatterns #DesignIdeas
What Equipment Will You Need
Besides your building materials (brick, gravel, and sand) the only equipment you will need is a sturdy wheelbarrow and shovels, a brick hammer and chisel, and a steel trowel.
Although you can use any flat item for levelling and smoothening edges (e.g. a straight timber beam), a carpenter’s level and line level are practical and useful.
To set the bricks evenly you can use pieces of plywood, but tile shops sell large-size spacers that are easier to use and inexpensive. #DIYTools #BuildingEquipment
Building Materials
Calculate the size of your patio space (in square metres) by multiplying the length by the width – for example, a 5m x 3m patio = 15 square metres (m2).
Add 10% to allow for errors and fillers (beginners should add extra). Please note that the quantities below are only a guide – if your bed is sloped, it may need more sand to level.
If your ground is “boggy”, it may need additional gravel for drainage. You may choose to add a layer of Bidem to prevent weeds from growing through, or special edging.
- Bricks – your size (m2). On average, there are 40-50 pavers per square metre.
- Gravel – your size (m2) x 0.15 (as an indicator, 2.5 tonnes of average gravel material will cover about 15m2).
- Bedding sand: size (m2) x 0.05 (as an indicator 750kg will cover about 20m2.)
- Jointing sand: a 40kg bag will cover about 15m2 of paving, depending upon the size of the joint spaces.
BuildingMaterials #PatioConstruction
This main article can be found here. This is a great article, and it would be of good information to people interested in India.
To order this product, you can visit our product page Durable Red Clay Pavers.